Заготовительный цех фаянсового завода
- Kirill Prilipskiy
- 29 нояб. 2016 г.
- 2 мин. чтения
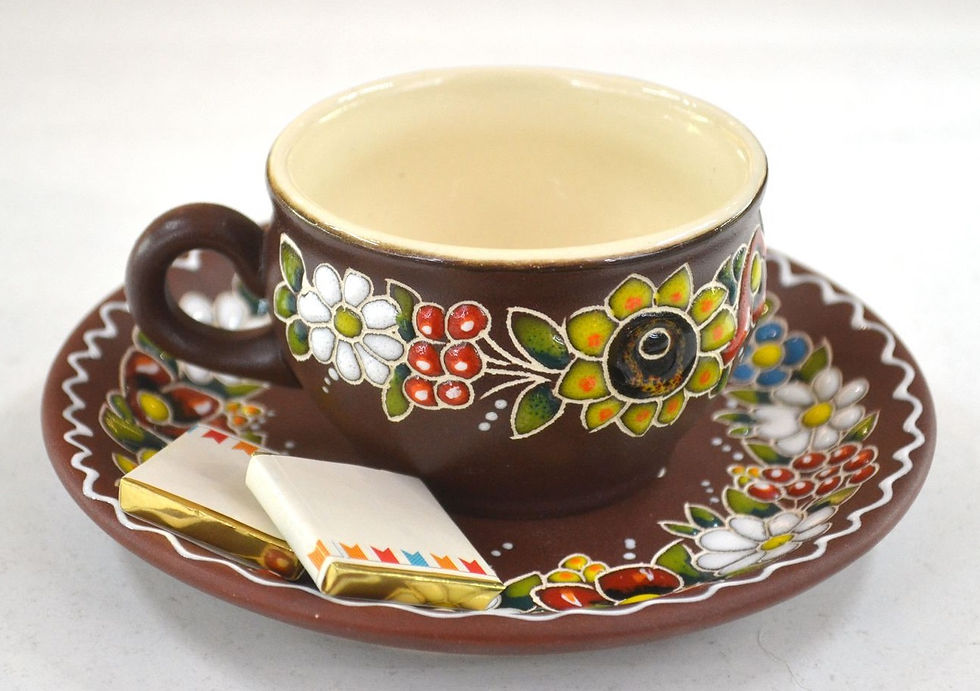
В состав всей фаянсовой посуды обязательно входят такие вещества как огнеупорная белая глина и кварц.
План расположения оборудования массозаготовительного цеха и механизированного склада сырья представлен ниже.

На плане:
1 - грейферный кран;
2 - грохот;
3 - глинорезки;
4 - монорельсовая ковшовая вагонетка;
5 - лифтовой подъемник;
6 - бегуны;
7 - ковшовые элеваторы;
8 - шаровые мельницы;
9 - горизонтальные мешалки;
10 - пропеллерные смесители;
11 - вибросита;
12 - мембранные насосы;
13 - расходные сборники;
14 - камерные фильтрпрессы;
15 - шнековые мялки;
16 - массохранилище;
17 - стиральный барабан;
18 - центрифуга;
19 - кулисное сушило для полотен;
20 - монорельсовые пути;
21 - монорельсовый поворотный круг,
22 - монорельсовая стрелка.
Вагоны с прибывающим на завод сырьем подаются внутрь склада, отметка пола которого лежит на 2 м ниже отметки головки рельса.
Сырье выгружается в разгрузочную траншею, идущую вдоль железнодорожной эстакады, и с помощью грейферного мостового крана укладывается в штабели по соответствующим отсекам склада.
Этим же краном глинистые материалы подаются в загрузочные отверстия глинорезок для предварительного измельчения, а кварцевый песок - к грохоту.
Переработанное сырье ковшовыми и бункерными монорельсовыми вагонетками транспортируется через лифтовой подъемник в завесочную, расположенную во втором этаже массозагоговительного цеха.
Дробление полевого шпата и входящего в состав массы фаянсового черепа производится на бегунах, работающих в замкнутом цикле с ситами-буратами. Просеянные материалы с помощью шнеков распределяются по бункерам.
После весовой дозировки компоненты массы на монорельсовых вагонетках подаются для дальнейшей переработки в отделение тонкого помола и приготовления жидкой массы. Здесь материалы подвергаются тонкому измельчению в шаровых мельницах мокрого помола; глина и каолины распускаются в воде в горизонтальных мешалках.
Из мельниц и мешалок глинистые суспензии сливаются в сборники-смесители, в которых производится интенсивное смешивание суспензий. Жидкая масса, содержащая все компоненты, подвергается ситовому обогащению на виброситах и ферромагнитной очистке в электромагнитных сепараторах, а затем перекачивается в расходные сборники.
Отсюда обогащенная жидкая масса с помощью мембранных насосов подается в камерные фильтры периодического действия, в которых производится ее обезвоживание до влагосодержания 21-23%.
Выгруженные из прессов коржи массы транспортируются к мялкам шнекового типа. Далее масса или направляется для вылеживания в массохранилище, расположенное под фильтрпрессами, или же подается в формовочный цех к вакуумным мялкам, в которых производится ее дезаэрирование.
Мойка, пропитка и сушка фильтрпрессных полотен осуществляется в специальной прачечной, оборудованной моечным барабаном, центрифугой для отжимания воды и кулисным сушилом.
Благодаря целесообразному расположению оборудования в цехе ликвидированы встречные движения и достигнута прямоточность производственного процесса, начиная от склада сырья и кончая подачей в фомовочный цех готовой массы.
Применение описанной схемы планировки представляется технологически более оправданным и рекомендуется при сооружении новых массозаготовительных цехов на фарфоровых и фаянсовых заводах.
Comments