План завода по производству лампочек
- Kirill Prilipskiy
- 1 июн. 2018 г.
- 4 мин. чтения

Чертежи ниже иллюстрируют общую схему производства ламп на заводе «Уэмбли» компании Osram.
Первый этап здания - трехэтажная конструкция шириной 80 футов (24 м) на 400 футов (120 м) длиной, при этом две трети площади помещения предназначены для хранения.
На первом этаже находились огромные запасы стеклянных ламп, что было необходимо благодаря очень высокой скорости нового типа стеклянных ламповых машин Westlake на соседнем сталелитейном заводе «Уэмбли», каждый из которых производил до 100 000 шт в день, и который должен был работать делая лампу того же типа в течение по крайней мере нескольких недель, чтобы обеспечить экономию от масштаба, которая необходима для минимизации затрат.
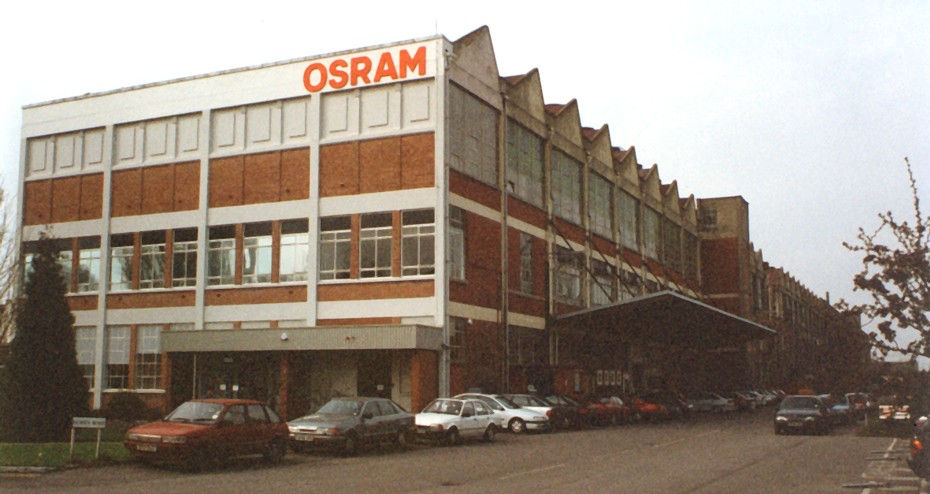
После поступления на конвейеры цоколи ламп подавались для автоматической промывки кислотой, а затем промывки в кипящей воде, сушки и подъема электрическим подъемником на этаж выше.

Также на первом этаже были представлены меньшие запасы всех других материалов, некоторые из которых были подготовлены для изготовления ламп.
Большие загрузочные двери включали грузовые автомобили, которые направлялись прямо в одну сторону завода в соответствующую часть хранилища, в то время как железнодорожный въезд проходил вдоль противоположной стороны, чтобы облегчить попадание большого объема и выход компонентов и готовых ламп.
Верхний этаж здания использовался для изготовления ламп и был примечателен тем, что вся его площадь была свободна от любых разделительных стен или колонн для поддержки крыши.
Это самое необычное сооружение привело к тому, что здание приобрело впечатляющий статус крупнейшего открытого производственного пространства на любой фабрике в мире.
Это позволяло компоновке производственных машин и транспортировки материалов с полной свободой от обычных препятствий, которые ухудшают гибкость большинства промышленных зданий и, как результат, стоимость готовой продукции.
При сохранении этого «священного прямоугольника» производственного пространства все вспомогательные требования, такие как лифты, лестницы, туалеты и т. д., были предоставлены в качестве внешних выступов из главного здания.
Как правило, такая обширная неподдерживаемая крыша привела к очень дорогостоящей стальной конструкции, но на Уэмбли этого избегали, делая крышу особенно легкой конструкции из-за устранения ее требования поддерживать вспомогательные конструкции и коммуникации, такие как электрические кабели и газопроводы.
На большинстве заводов подвод коммуникаций для каждой машины осуществлялся сверху, но завод Уэмбли имел другие решения, при котором коммуникации проходили вдоль потолка пола под производственным пространством.
Верхний этаж был собран из новой клеточной кирпичной структуры, покрытой паркетным полом из твердых пород древесины, и это позволило просто удалить половую ячейку в любом месте без ущерба для структурных свойств, так что на каждую машину могли бы быть поданы газы, вода и электрические сети из-под пола.
В результате эта фабрика получила свободную планировку, позволяющую четко и беспрепятственно смотреть с одного конца на другой.
Кроме того, полы всех уровней были изначально выгнуты, так что любые утечки воды из машин или спринклерной системы автоматически сливались в стороны, а не собирались на полу, как это часто бывает даже на современных заводах, чьи полы никогда не были абсолютно плоскими.
Изготовление ламп связано с детальным сбором мелких деталей с предельной точностью, а освещение на высоком уровне имеет важное значение.
Чтобы избежать увеличения эксплуатационных расходов, прибегая к использованию собственного продукта для обеспечения искусственного освещения, дизайнеры «Уэмбли» настаивали на прозрачной крыше в сочетании с почти полностью застекленными боковыми стенками вокруг производственного пространства верхнего этажа.
Это оказалось чрезвычайно эффективным, использование электрического света не требуется перед закатом даже в пасмурные дни.
Чтобы облегчить непрерывное производство в ночное время, оригинальная схема освещения состояла из 750-ваттных ламп GLS, подвешенных с частыми интервалами на 18 футов (5,5 м) над уровнем пола, чтобы обеспечить среднюю освещенность 12 фут-свечей.
Естественно, это было модернизировано до флуоресцентной системы после изобретения GEC и позже коммерциализации этого более эффективного источника света.
Из-за бесконечных газовых процессов нагрева и других высокотемпературных процессов, связанных с изготовлением ламп, фабрики для производства этой статьи часто становятся душным адом в течение летних месяцев, и это не способствует удовлетворенности работникам или качеству работы.
Эти проблемы обычно можно извлечь, предоставив полноцветную конструкцию, например, на «Уэмбли».
Чтобы свести к минимуму проблемы с нагревом, это длинное и узкое здание было ориентировано почти точно на север-юг, и только передняя южная стена была кирпичной конструкции, чтобы избежать чрезмерного нагрева и солнечного блика.
Кроме того, была предусмотрена высокая крыша, обеспечивающая сбор и вывод нагретого воздуха.
Это, возможно, сделало здание непригодным для зимнего производства любого другого продукта, и, возможно, дополнительные радиаторы должны были быть предусмотрены вдоль боковых стенок - но на заводе с большим объемом ламп обычно не хватает труда, чтобы сохранить тепло!
После сборки ламп средний этаж выполнял свою функцию склада готовой продукции, готовые лампы транспортировались вниз через гравитационные желоба.
Для отправки лампы перевозили на первый этаж и далее автомобильным и железнодорожным транспортом в различные склады компании по всей стране для окончательного распределения оптовикам и конечным потребителям.
Вскоре после его строительства здание несколько расширилось, что позволило утроить площадь в течение пяти лет.
Непосредственно перед второй мировой войной планировалось удвоить размеры производственных площадей, построив параллельный дубликат главного здания, причем два из них были соединены друг с другом в нескольких мостовых точках, образуя гигантскую H-образную структуру.
Строительство второго блока началось, но позже было заброшено, и что было построено, было разрушено, чтобы освободить место для военных бомбардировщиков военного времени.
Позже этот район был преобразован для обеспечения парковки автомобилей.
Считается, что причина изменения плана связана с увеличением дефицита фабричного труда из-за растущего благосостояния Северо-западного Лондона.
Кстати, завод работал в три смены: полная смена с 9 утра до 5 вечера, короткая смена с 18:00 до 20:00, в основном укомплектованная местными замужними дамами, а затем полная смена с 22 часов ночи.
Мертвые периоды между этими сдвигами обеспечивали возможность регулярного технического обслуживания оборудования.
Comentários